Porosity in Welding: Identifying Common Issues and Implementing Best Practices for Prevention
Porosity in welding is a pervasive problem that usually goes unnoticed up until it creates substantial problems with the integrity of welds. This common defect can compromise the toughness and sturdiness of welded structures, posing safety and security threats and leading to expensive rework. By recognizing the origin of porosity and carrying out efficient avoidance strategies, welders can considerably boost the high quality and reliability of their welds. In this conversation, we will explore the essential factors adding to porosity formation, examine its damaging effects on weld performance, and go over the best techniques that can be adopted to reduce porosity occurrence in welding processes.
Typical Reasons of Porosity

Another constant offender behind porosity is the visibility of contaminants externally of the base steel, such as oil, oil, or rust. When these contaminants are not properly removed before welding, they can evaporate and become entraped in the weld, triggering defects. Moreover, making use of filthy or damp filler products can present contaminations right into the weld, adding to porosity concerns. To minimize these typical reasons for porosity, thorough cleaning of base steels, appropriate shielding gas selection, and adherence to ideal welding criteria are vital techniques in achieving top notch, porosity-free welds.
Influence of Porosity on Weld High Quality

The presence of porosity in welding can considerably compromise the structural integrity and mechanical properties of welded joints. Porosity develops gaps within the weld metal, deteriorating its overall stamina and load-bearing capability.
Welds with high porosity degrees tend to exhibit reduced influence strength and lowered capability to deform plastically prior to fracturing. Porosity can hamper the weld's capacity to successfully send pressures, leading to early weld failure and potential safety threats in critical frameworks.
Finest Practices for Porosity Avoidance
To enhance the architectural honesty and high quality of bonded joints, what particular measures can be carried out to reduce the event of porosity during the welding process? Using the right welding strategy for the specific product being bonded, such as adjusting the welding angle and gun setting, can even more protect against porosity. Routine inspection of welds and immediate removal of any issues determined throughout the additional hints welding process are important techniques to avoid porosity and produce high-quality welds.
Significance of Appropriate Welding Techniques
Implementing correct welding techniques is critical in ensuring the architectural stability and quality of bonded joints, building on the structure of effective porosity avoidance measures. Welding techniques directly influence the overall strength and durability of the welded structure. One crucial facet of appropriate welding strategies is preserving the correct heat input. Too much heat can bring about boosted porosity because of the entrapment of gases in the weld pool. Alternatively, not enough heat might result in article source insufficient combination, developing prospective weak points in the joint. In addition, using the ideal welding criteria, such as voltage, present, and travel rate, is important for achieving audio welds with minimal porosity.
Furthermore, the selection of welding process, whether it be MIG, TIG, or stick welding, must line up with the certain demands of the job to make certain ideal results. Proper cleaning and preparation of the base steel, along with choosing the right filler product, are additionally vital parts of skillful welding strategies. By adhering to these finest practices, welders can decrease the danger of porosity formation and create high-grade, structurally audio welds.
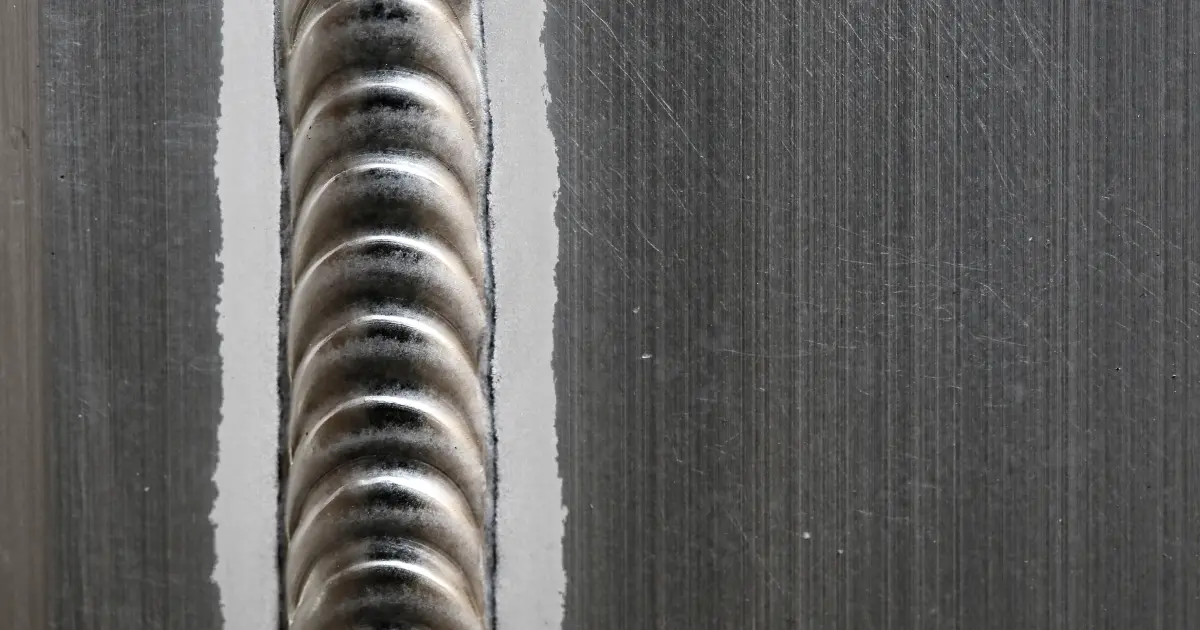
Examining and High Quality Control Procedures
Evaluating treatments are necessary to identify and protect against porosity in welding, making sure the toughness and longevity of the final item. Non-destructive testing techniques such as ultrasonic screening, radiographic testing, and aesthetic inspection are typically used to recognize potential flaws like porosity.
Post-weld examinations, on the other hand, analyze the last weld for any type of issues, consisting of porosity, and validate that it satisfies specified criteria. Carrying out an extensive quality control strategy that consists of thorough testing treatments and official website assessments is extremely important to reducing porosity issues and guaranteeing the general high quality of bonded joints.
Final Thought
To conclude, porosity in welding can be a common issue that impacts the quality of welds. By identifying the common sources of porosity and carrying out finest techniques for prevention, such as proper welding strategies and testing procedures, welders can make certain high top quality and reputable welds. It is necessary to focus on avoidance techniques to decrease the occurrence of porosity and keep the stability of welded frameworks.
Comments on “Professional Guidance on What is Porosity in Welding and Just How to Address It”